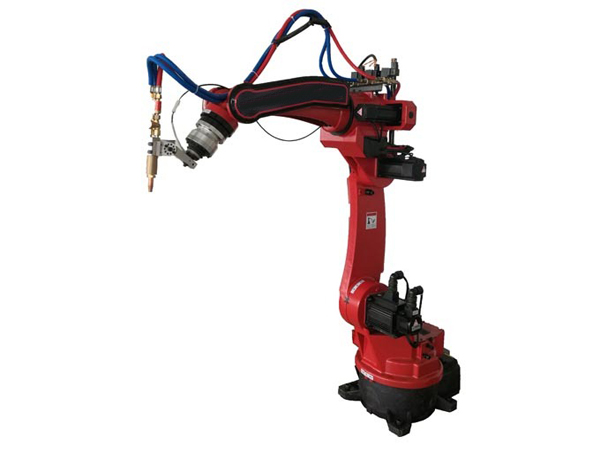
Cutting robot
- Commodity name:Cutting robot
- Manufacturer: Xinbao Intelligent
Product Details
The composition of the cutting robot system:
The cutting robot consists of three main parts: the cutting robot arm, the robot control system, and the welding groove programming and nesting software.
Mechanical arm part: Independently designed and developed, obtaining a cutting mechanical arm, adopting a connecting rod structure, concentric axis and joint parallel design, using high-precision gapless planetary robot reducer, using Panasonic and Yaskawa high inertia servo drives and motors, adopting a direct connection between reducer and motor, the overall motion accuracy reaches ± 0.2mm.
Control part: Independently developed cutting robot controller (control system) and built-in plasma intelligent arc voltage adjustment system, including FastFNC flat groove cutting control system, FastPBC pipe intersection line groove cutting system, and H-beam and ball flat steel groove cutting control system.
Software part: Three sets of offline programming software have been developed to meet the needs of cutting robots for cutting flat plates, pipes, and steel sections:
1. Flat groove programming and nesting software, which writes the flat groove welding process into the software, directly realizing offline programming, whole plate nesting, and CNC cutting of flat grooves.
2. The software for cutting the intersection line of pipes and the steel structure groove of pipe racks is used to write the welding processes of Chinese CWS and American AWS pipes into the software, realizing offline programming and one-time forming cutting of pipe welding grooves.
3. Steel cutting programming and nesting software, capable of completing offline programming and CNC cutting for various types of steel cutting in one go.
The composition of the cutting robot system is as follows:
1. Specialized robotic arm for cutting robots
2. High precision gapless planetary reducer
3. Photoelectric limit for groove cutting motion
4. Mechanical limit for bevel cutting motion
5. A set of specialized debugging tools for robotic arms
1. The robotic arm adopts a concentric axis transmission method, which not only solves the problem of two eccentric axes of the linkage mechanism not being concentric, but also solves the problem of plasma cable winding in infinite or finite rotation bevel mechanisms, effectively improving the quality of bevel cutting.
2. The robotic arm adopts a high-precision gapless planetary reducer with high repeatability and positioning accuracy, including reverse clearance of several arc minutes. In addition, all robotic arms are processed using CNC machine tools, with an overall motion accuracy of ± 0.20mm, ensuring the accuracy of groove cutting. The motion accuracy of a regular bevel cutting machine is within ± 2.00mm.
3. The left and right swing of the robotic arm can reach plus or minus 60 degrees, and the front and rear swing can reach plus or minus 45 degrees, which maximally meets the cutting standards of the welding process, reduces the amount of manual polishing, and improves the production efficiency of cutting and welding for users.
4. The robotic arm is equipped with a dedicated precision gauge, which facilitates users and cutting machine engineers to quickly and easily use and detect the height of the cutting gun, ensuring cutting quality.
Built in intelligent arc voltage adjustment system
Based on the detection of arc pressure in vertical cutting of flat plates, an intelligent arc pressure adjustment system has been developed for groove cutting, which automatically collects arc pressure values, adapts to various groove types and arc pressure requirements, and adapts to the influence of new and old nozzle electrodes on arc pressure, effectively solving the problem of arc pressure control in flat groove cutting. No manual intervention is required, the system will automatically collect and process arc pressure, and automatically control the height of groove cutting.
Cooperate with the flat groove programming nesting software to achieve more reasonable timing selection for adjusting the height switch. Using PID algorithm combined with servo motor to control height, the speed adjustment is more precise, avoiding the possibility of arc breakage.
The built-in intelligent arc voltage adjustment system can adapt to the vast majority of high-frequency or low-frequency high-voltage arc starting plasma power supplies on the market, including Haibao, Victor, Kelbe, and Issa plasma power supplies.
Control system
The CNC system adopts a dual processor structure, and the front-end is an industrial grade PC104 motherboard running Microsoft Windows system, providing a feature rich and easy to search user interface; The backend adopts a dedicated motion control digital processing chip (DSP) to provide more powerful and closely controlled high-speed and accurate axis motion and complex machine logic, greatly improving processing speed, anti-interference ability, system performance, and system stability.
Provides up to 8-axis control, capable of controlling digital PWM, analog servo, stepper motors, etc., with advanced control functions including PID regulation, S-curve start stop, feedforward speed control, gantry double-sided drive, etc.
The flat bevel CNC cutting machine uses a flat cutting system, paired with FastCAM bevel software, to achieve difficult bevel cutting such as variable bevel, internal bevel, and external bevel without external cutting ears at corners. The corners are sharper and the internal angles are smoother.
The CNC cutting machine for pipe intersecting lines uses a pipe intersecting line cutting system, combined with pipe intersecting lines and pipe frame steel structure software, to achieve the construction of various conveying pipelines and pipe frame steel structure projects, especially in the construction of pipe frame steel structures on offshore platforms, meeting the requirements of AWS welding technology in the United States.
The flat groove cutting system shares hardware with the pipe intersecting line cutting system, allowing users to easily switch between the two cutting types of pipe plates. Depending on the customized rack, it can be used to produce a CNC flame plasma cutting machine that is dual-use for pipe plates.
The control system adheres to the spirit of simple and efficient user experience, and cooperates with the cutting code generated by the groove programming nesting software to analyze the cutting area, cutting length, groove information, corner angle, etc. from the code, so as to automatically perform a series of cutting process operations such as corner acceleration and deceleration, arc deceleration, no mouse ear deviation, and internal angle advance deviation, greatly reducing the complexity of operation. With the use of intelligent arc pressure, groove cutting becomes a reality, eliminating the need for secondary manual or mechanical polishing, and can be directly welded using robots.
Key words:
Online Consultation