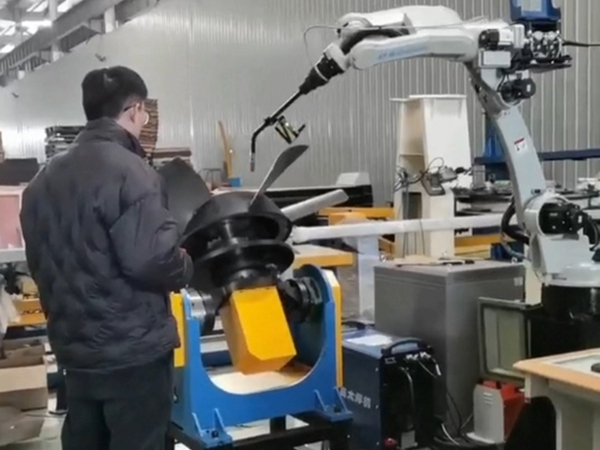
Automated Welding Workstation for Centrifugal Fan Impeller
- Commodity name:Automated Welding Workstation for Centrifugal Fan Impeller
- Manufacturer: Xinbao Intelligent
Product Details
1、 Introduction to Welding Workstation
This system equipment consists of a welding robot system, a dual axis positioner, a laser vision guidance system, and a welding system. This device is used to replace manual completion of automated welding of centrifugal fan impellers. No manual intervention is required during the welding process, and manual operation only requires loading before welding and unloading after welding. The welding trajectory is automatically guided by laser vision, and the welding height, front and back, left and right, and posture rotation are automatically adjusted.
1) On site environmental requirements
1) Environmental temperature: 0-45 ℃; 2. Relative humidity: 20-80% RH; 3. Vibration: Vibration acceleration less than 0.5g;
4) Power supply: three-phase 380V; Frequency: 50Hz;
Voltage fluctuation range:+10%, -15%;
Single station capacity: Power supply for robot welding: 35KVA;
5) Compressed air: 5kgf/cm2 (requires filtered water and oil);
6) There is no corrosive gas present on site.
2. Product and Requirements
1) Pre welding status: The workpiece has been spot welded in the previous process;
2) Welding method: Gas shielded welding (80% Ar+20% CO2);
3) Welding products: fan impeller; The rotation diameter range of the workpiece is centrifugal impeller 400~1200mm; The maximum weight of the workpiece is 400KG (including fixtures).
Larger than this specification can be customized according to requirements.
4) The welded and positioned parts of the workpiece are free of defects such as burrs, rust, oil stains, etc. that affect the welding quality.
5) Accuracy requirement: The gap between butt welds between parts should be less than 2.5mm, and the gap between corner welds should be less than 2.5mm.
6) Post welding condition: Finished product (if there are welding blind spots due to interference between the fixture, workpiece, and welding gun, they will be manually repaired).
3. Overall Introduction
The system consists of a six axis welding robot, Outai welding power supply, P-type positioner, electrical control system, laser guided vision system, customized welding gun, etc.
This workstation has signal interlocking and mutual locking between various actions to prevent misoperation and improve the overall performance of the workstation.
4、 Process flow
1. The general requirements for workpieces are to adapt to robot welding production and improve work efficiency. Precautions for workpieces:
1) The gap between butt welds and corner welds between parts is less than 0.5mm of the welding wire radius;
2) The surface of the workpiece welding position should be free of oil, rust, and dirt to avoid defects such as porosity. 2. Operation process
3) Manually place the workpiece on the workbench for positioning and clamping, and press the "start" button; B、 The robot starts up and reaches the welding position, completing the welding process;
4) Reset the robot after welding is completed;
5) Manually unload the workpiece and complete one work cycle.
Key words:
Online Consultation