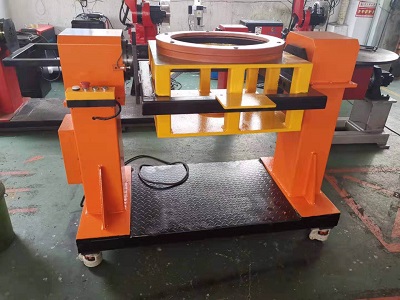
Robot U-shaped dual axis positioner
- Commodity name:Robot U-shaped dual axis positioner
- Manufacturer: Xinbao Intelligent
Product Details
Robot positioner is a specialized welding auxiliary equipment, suitable for welding displacement in rotary work to obtain ideal machining positions and welding speeds. It can be used in conjunction with operating machines and welding machines to form an automatic welding center, and can also be used for workpiece displacement during manual operations. The worktable rotation adopts a frequency converter for stepless speed regulation, with high speed regulation accuracy. The remote control box can achieve remote operation of the workbench, and can also be connected to the control system of the operating machine and welding machine to achieve linkage operation.
The welding robot positioner is generally composed of the rotary mechanism and the turnover mechanism of the workbench. The workpiece fixed on the workbench can reach the required welding and assembly angle through the lifting, turnover and rotation of the workbench. The workbench rotation is variable frequency stepless speed regulation, which can obtain satisfactory welding speed.
Choose:
Usually, when designing an electric driven robot positioner scheme, it is necessary to choose the mechanical transmission mode and corresponding transmission mechanism between the motor and the worktable. Before selecting, clarify the following requirements based on the characteristics of the assembly and welding process:
(1) Functional requirements for robot displacement machinery: Refers to the actions that the robot displacement machinery should be able to perform, such as translation, lifting, or rotation. If it is translation, is it linear translation or curved translation; If it is a rotary motion, whether it is continuous rotation or intermittent flipping, etc;
(2) Requirements for sports speed: specify whether it is fast or slow, whether it is constant speed or variable speed, whether it is step variable speed or continuously variable speed;
(3) Requirements for transmission stability and accuracy: Robot positioners used for automatic welding require high transmission accuracy, in which case worm gear transmission and gear transmission can be selected;
(4) Requirements for self-locking, overload protection, and vibration absorption capabilities: For general lifting, flipping, and transmission systems with the risk of overturning, the transmission mechanism must have self-locking capabilities. There may be multiple transmission modes and their corresponding transmission mechanisms, and in this case, it is necessary to comprehensively consider the transmission power, compactness, transmission efficiency, and manufacturing cost between them before selecting the optimal one.
Structure:
① Double column single rotary robot positioner: This type of robot positioner is suitable for welding rectangular structural components of construction machinery such as the rear frame of loaders and roller frames. Its main feature is that one end of the column is driven by a motor to rotate the working device in one direction, and the other end is driven by the main driving end. The two side columns can be designed to be adjustable to accommodate products of different specifications. The disadvantage of this type of robot positioner is that it can only rotate in one circumferential direction. When selecting, attention should be paid to whether the weld seam form is suitable.
② U-shaped double seat head and tail double rotation type: Compared with one type of robot displacement type, the welded structural components on the basis of the two types add another degree of rotational freedom in another space.
③ L-type dual rotation welding robot positioner: This type of robot positioner has an L-shaped working device with two degrees of rotational freedom, and can rotate freely within ± 360 ° in both directions. Compared with other types of robot positioners, this robot positioner has good openness and is easy to operate. The L-type robot positioner has been successfully used in the welding of the front frame of the loader, and the use effect is very good, which is highly welcomed by on-site operators.
④ C-type double rotation welding robot positioner: The C-type rotation form is the same as the L-type machine, but for the convenience of clamping specific designs, the working device of the robot positioner is slightly changed according to the shape of the structural components. This type of welding robot positioner is suitable for welding the buckets of loaders and excavators.
⑤ Seat type universal robot positioner: The worktable of the seat type welding robot positioner has a degree of freedom for overall flipping, which can flip the work to the ideal welding position for welding. In addition, the workbench also has a degree of rotational freedom. This type of robot positioner is suitable for welding small welding parts of construction machinery and some small and complex structures such as pipes, shafts, and disks.
Key words:
Online Consultation