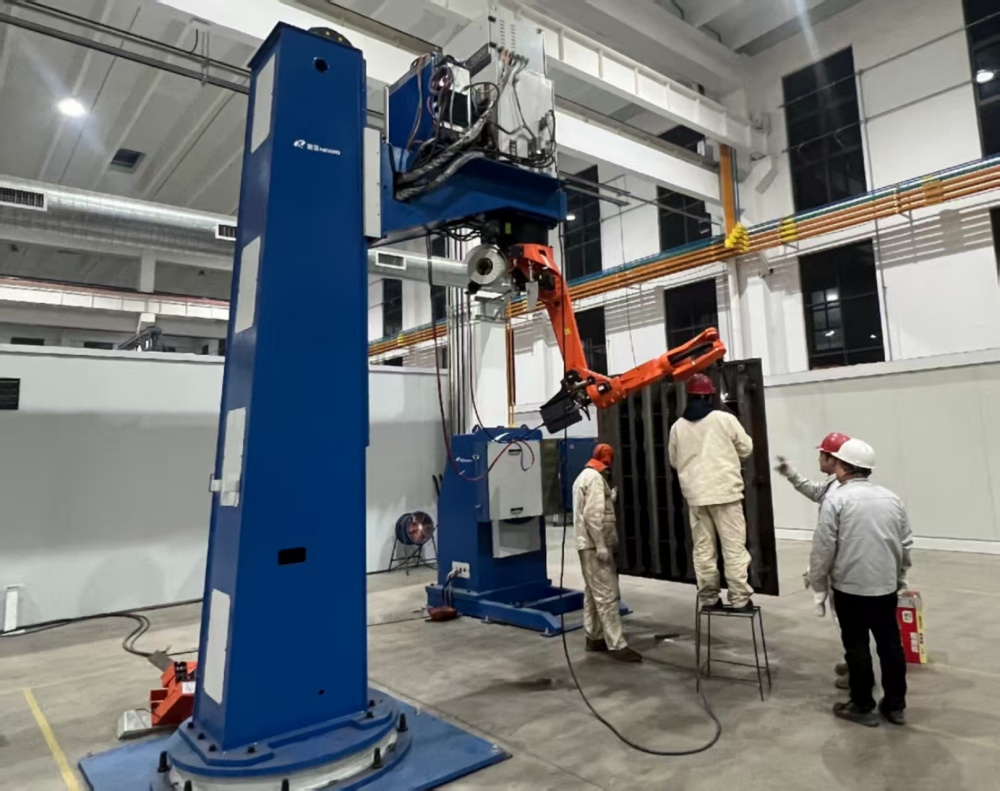
Welding robot
- Commodity name:Welding robot
- Manufacturer: Xinbao Intelligent
Product Details
Welding Robot Product Introduction:
1. Welding robot technology, as a typical representative and main technical implementation method of manufacturing technology, has played an important role in improving product quality, enhancing production efficiency, improving working environment, and increasing automation level.
2. Robot system integration is based on industrial robots as the core unit, combined with good welding equipment, welding process technology, and system engineering technology. With its wide application range, flexible and diverse processes, high precision of processed products, stable quality, high degree of automation, flexibility, and intelligence, it is increasingly widely used in various industries and has become an important component of modern welding industry.
Reasonable solutions can effectively improve welding production efficiency
Can ensure the stability and consistency of the welding process, ensuring stable and controllable welding quality
The robot system integration technology is mature, the system operation reliability is high, and the equipment failure rate is low
The linkage between robots and workpieces, as well as the collaborative work between robots, can ensure a suitable welding posture and adjust welding process parameters in real time according to the special conditions of the workpiece to improve welding quality and reduce post welding deformation of the workpiece
Easy to achieve automation of welding production lines, with strong flexibility, suitable for enterprise product changeover
Reduce the labor intensity of workers and improve the working environment
Enhance the planning and foresight of enterprise production management
Composition and characteristics of welding robots:
Welding robots mainly include two parts: robots and welding equipment
The robot consists of a robot body and a control cabinet (hardware and software). Arc welding equipment consists of welding power supply, wire feeder, welding gun and other parts.
The vast majority of welding robots have 6 axes, among which axes 1, 2, and 3 can deliver the end welding gun to different spatial positions, while axes 4, 5, and 6 solve the different requirements of welding gun posture
The arc welding robot is a low load robot, with a typical load of 3-10kg
Fast running speed, reducing non working time
High repeatability accuracy, allowing for repeated work while ensuring welding position accuracy after one trial teaching
Multiple welding gun movement modes can be achieved through software programming, such as swing welding, multi-layer and multi pass welding, etc
Contact positioning, automatic search for the starting position of the weld seam, arc tracking, and automatic arc reignition function
Robot systems can generally externally control the coordinated motion of multiple external axes to expand welding space, obtain suitable welding positions, and welding postures.
Common equipment and devices for robot welding:
Various types of positioners
Installation and expansion equipment for various types of robots
Workpiece positioning clamping device
Gun cleaning and wire cutting equipment.
Requirements for robot welding:
Good consistency between workpiece size and weld seam gap
High requirements for the appearance and precision of product welds
Forming mass-produced products
Small batch size but diverse varieties, quick changeover, uncertain future products
Products with diverse weld forms that are difficult to weld with traditional specialized machines.
Key words:
Online Consultation