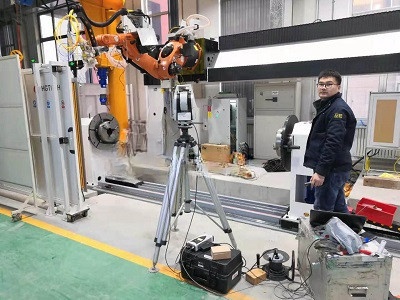
Welding robot system
- Commodity name:Welding robot system
- Manufacturer: Xinbao Intelligent
Product Details
Characteristics of Welding Robot System:
With the development of electronic technology, computer technology, numerical control, and robot technology, automatic welding robots have become increasingly mature since their use in production in the 1960s. They mainly have the following advantages:
1) Stabilize and improve welding quality, and be able to reflect welding quality in numerical form;
2) Improve labor productivity;
3) Improve the labor intensity of workers and enable them to work in hazardous environments;
4) Reduced the requirements for workers' operational skills;
5) Shortened the preparation period for product modification and replacement, and reduced the corresponding equipment investment.
Therefore, it is widely used in various industries.
Structural design of welding robot system:
Due to the fact that the designed welding robot operates in a quasi planar and narrow space environment, in order to ensure that the robot can track and automatically weld the weld seam based on the deviation information of the arc sensor, it is required that the designed robot should have a compact structure, flexible movement, and stable operation. In response to the characteristics of narrow spaces, a small mobile welding robot was developed in this article. Based on the motion characteristics of each structure of the robot, a modular design method was used to divide the robot mechanism into three parts: a wheeled mobile platform, a welding torch adjustment mechanism, and an arc sensor. Among them, the wheeled mobile platform, due to its large inertia and slow response, mainly performs rough tracking of the weld seam. The welding torch adjustment mechanism is responsible for accurate tracking of the weld seam, and the arc sensor completes real-time identification of weld deviation. In addition, the robot controller and motor driver are integrated and installed on the robot mobile platform, making its volume smaller. At the same time, in order to reduce the impact of dust on moving parts in harsh welding environments, a fully enclosed structure is adopted to improve its system reliability.
Maintenance and upkeep of welding robot system:
1、 Daily inspection and maintenance
1. Wire feeding mechanism. Including whether the wire feeding distance is normal, whether the wire feeding catheter is damaged, and whether there are any abnormal alarms. 2. Is the gas flow rate normal. 3. Is the welding gun safety protection system functioning properly. (Prohibit turning off welding gun safety protection work) 4. Check if the water circulation system is working properly. 5. Test TCP (it is recommended to develop a test program and run it after each shift handover)
2、 Weekly inspection and maintenance
1. Clean all axes of the robot. 2. Check the accuracy of TCP. 3. Check the residual oil level. 4. Check whether the zero positions of each axis of the robot are accurate. 5. Clean the filter screen behind the welding machine water tank. 6. Clean the filter screen at the compressed air inlet. 7. Clean the impurities at the nozzle of the welding gun to avoid blocking the water circulation. 8. Clean the wire feeding mechanism, including the wire feeding wheel, wire pressing wheel, and wire guide tube. 9. Check whether the hose bundle and guide wire hose are damaged or broken. (It is recommended to remove the entire hose bundle and clean it with compressed air) 10. Check whether the safety protection system of the welding gun is normal, and whether the external emergency stop button is normal.
3、 Monthly inspection and maintenance
1. Lubricate each axis of the robot. Add white lubricating oil to axes 1-6. Oil number 86E006. Add butter to the red oil nozzle on the RP positioner and RTS track. Oil number: 86K007 3. Add gray conductive grease to the blue fuel nozzle on the RP positioner. Oil number: 86K004 4. Add lubricating oil to the needle roller bearing of the wire feeding wheel. (A small amount of butter is sufficient) 5. Clean the gun cleaning device and add lubricating oil to the pneumatic motor. (Ordinary engine oil is sufficient) 6. Clean the control cabinet and welding machine with compressed air. 7. Check the cooling water level of the welding machine water tank and replenish the coolant in a timely manner (pure water with a little industrial alcohol is sufficient). 8. In addition to completing tasks 1-8, perform all weekly inspection items.
Key words:
Online Consultation