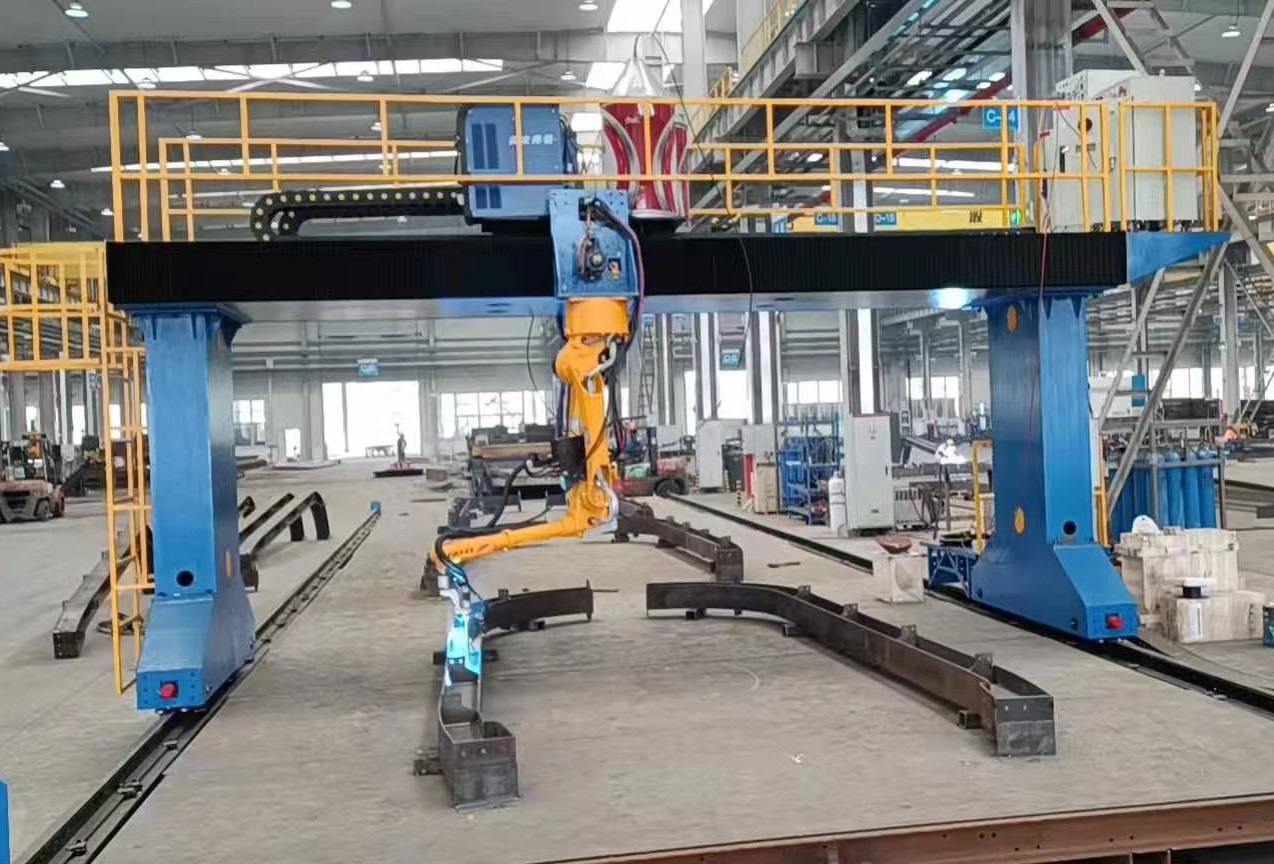
Welding robot arm
- Commodity name:Welding robot arm
- Manufacturer: Xinbao Intelligent
Product Details
Introduction to Welding Robot:
With the development of electronic technology, computer technology, numerical control, and robot technology, automatic welding robots have become increasingly mature since their use in production in the 1960s. They mainly have the following advantages:
1) Stabilize and improve welding quality, and be able to reflect welding quality in numerical form;
2) Improve labor productivity;
3) Improve the labor intensity of workers and enable them to work in hazardous environments;
4) Reduced the requirements for workers' operational skills;
5) Shortened the preparation period for product modification and replacement, and reduced the corresponding equipment investment.
Therefore, it has been widely applied in various industries.
Characteristics of welding robotic arms:
Spot welding does not have very high requirements for welding robots. Because spot welding only requires point position control, there are no strict requirements for the movement trajectory of the welding tongs between points, which is also the reason why robots were only used for spot welding earlier. Spot welding robots not only need to have sufficient load capacity, but also need to move quickly, move smoothly, and position accurately between points to reduce displacement time and improve work efficiency. The load capacity required for spot welding robots depends on the form of welding tongs used. For welding tongs separated from transformers, a robot with a load of 30-45kg is sufficient. However, this type of welding tongs is not conducive to robots inserting the tongs into the workpiece for welding due to the long secondary cable and high energy loss; On the other hand, the cable keeps swinging with the robot's movement, causing rapid damage to the cable. Therefore, the use of integrated welding tongs is gradually increasing. This welding tongs, together with the transformer, weigh around 70kg. Considering that robots need to have sufficient load capacity to deliver welding tongs to spatial positions with high acceleration for welding, heavy-duty robots with a load of 100-150kg are generally selected. In order to meet the requirements of short distance and rapid displacement of welding tongs during continuous spot welding. The new heavy-duty robot has added the ability to complete a 50mm displacement within 0.3 seconds. This places higher demands on the performance of the motor, the computing speed and algorithm of the microcomputer.
Structural design of welding robot arm:
Due to the fact that the designed welding robot operates in a quasi planar and narrow space environment, in order to ensure that the robot can track and automatically weld the weld seam based on the deviation information of the arc sensor, it is required that the designed robot should have a compact structure, flexible movement, and stable operation. In response to the characteristics of narrow spaces, a small mobile welding robot was developed in this article. Based on the motion characteristics of each structure of the robot, a modular design method was used to divide the robot mechanism into three parts: a wheeled mobile platform, a welding torch adjustment mechanism, and an arc sensor. Among them, the wheeled mobile platform, due to its large inertia and slow response, mainly performs rough tracking of the weld seam. The welding torch adjustment mechanism is responsible for accurate tracking of the weld seam, and the arc sensor completes real-time identification of weld deviation. In addition, the robot controller and motor driver are integrated and installed on the robot mobile platform, making its volume smaller. At the same time, in order to reduce the impact of dust on moving parts in harsh welding environments, a fully enclosed structure is adopted to improve its system reliability.
Equipment for welding robots:
The welding equipment of spot welding robots adopts integrated welding tongs, and the welding transformer is installed behind the welding tongs, so the transformer must be as small as possible. For transformers with smaller capacity, 50Hz AC can be used, while for transformers with larger capacity, inverter technology has been adopted to convert 50Hz AC into 600-700Hz AC, reducing the volume and weight of the transformer. After transformation, it can be directly welded with 600-700Hz AC power, or it can be rectified again and welded with DC power. The welding parameters are adjusted by a timer, as shown in Figure 1b. The new timer has been computerized, so the robot control cabinet can directly control the timer without the need for additional interfaces. The welding tongs of spot welding robots usually use pneumatic welding tongs, and the opening between the two electrodes of the pneumatic welding tongs is generally only two strokes. And once the electrode pressure is set, it cannot be changed arbitrarily. In recent years, a new type of electric servo spot welding tongs has emerged. The opening and closing of the welding tongs are driven by servo motors and feedback from the encoder, allowing the opening degree of this welding tongs to be arbitrarily selected and pre-set according to actual needs. And the clamping force between the electrodes can also be infinitely adjusted. This new electric servo spot welding tongs have the following features
Advantages of welding robotic arms:
1) The welding cycle of each welding point can be significantly reduced because the opening degree of the welding tongs is accurately controlled by the robot, and the robot's movement between points allows the welding tongs to start closing; After welding a little bit, the welding tongs can be opened while the robot can move, without waiting for the robot to be in place before closing the tongs or for the tongs to fully open before the robot moves;
2) The opening degree of the welding tongs can be adjusted arbitrarily according to the condition of the workpiece, as long as there is no collision or interference, the opening degree should be minimized as much as possible to save the opening degree of the welding tongs and the time occupied by the opening and closing of the welding tongs.
3) When the welding tongs are closed and pressurized, not only can the pressure be adjusted, but also the two electrodes are gently closed to reduce impact deformation and noise.
Key words:
Online Consultation